Durability is one of the most crucial elements when purchasing or constructing a home. After all, purchasing a house is a significant investment that should pay off in the long run. Prefabricated homes have grown in favor recently as a more affordable housing and speedy alternative to conventional building techniques. However, how durable is a prefabricated house when compared with a traditional home?
Prefab homes may survive for many years and resist harsh weather and natural disasters when built with high-quality materials and care. The quality of the materials used, the design and building methods, and maintenance all significantly affect how long a prefabricated home will last.
Read on to learn more about the durability of prefab homes and what to consider before purchasing.
Quick Navigation
- The Importance of Durability in Prefab Houses
- Different Materials Used in Prefabricated Houses
- Construction and Design of Prefabricated Houses
- Factors that Affect the Durability of Prefabricated Houses
- Maintenance and Repair of Prefabricated Houses
- Conclusion
The Importance of Durability in Prefab Houses
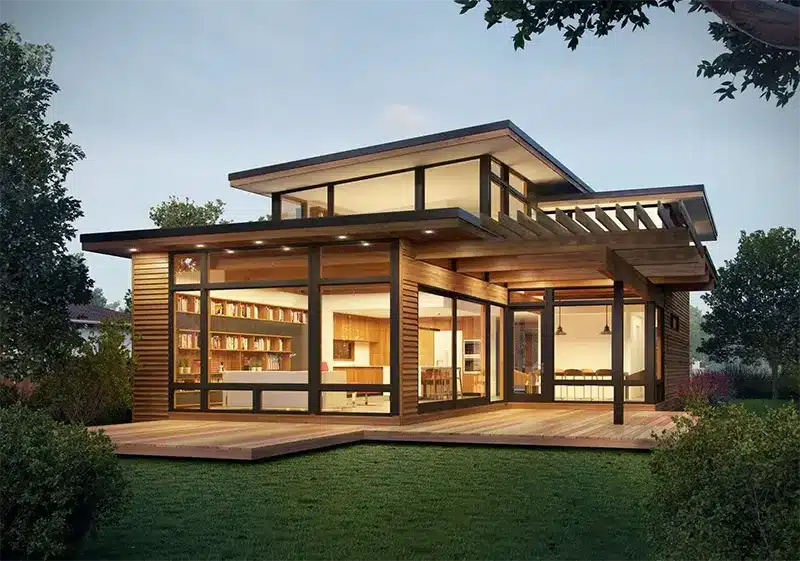
A prefabricated house, often known as a prefab home, is a kind of housing that is built off-site in a factory or manufacturing facility before being shipped and put together at its ultimate location.
The home is constructed on-site in components known as modules or panels that are meant to join together seamlessly to form the whole structure.
Prefabricated modular homes may be constructed out of a variety of materials, such as wood, steel, concrete, or a combination of these.
Consideration of durability is essential when it comes to prefab homes. A sturdy prefabricated home may provide long-term advantages and guarantee a pleasant living environment for its occupants.
A prefabricated modular house has several benefits, including resistance to extreme weather and natural calamities.
These homes are built in a controlled setting with premium components and exact specifications. They are often more robust and more durable than conventional dwellings constructed on-site.
Homeowners, especially those who reside in regions vulnerable to extreme weather disasters, may find comfort in its durability.
Well-built prefab homes may hold their worth over time and grow in value, giving homeowners a return on their investment.
Homeowners may ensure that their prefab house is a treasured asset for many years by putting durability first.
Different Materials Used in Prefabricated Houses
Some of the most typical components for prefabricated home building are the following:
Wood: For prefab homes, wood is a common material since it is portable and adaptable. It also has solid insulating qualities and is a renewable resource.
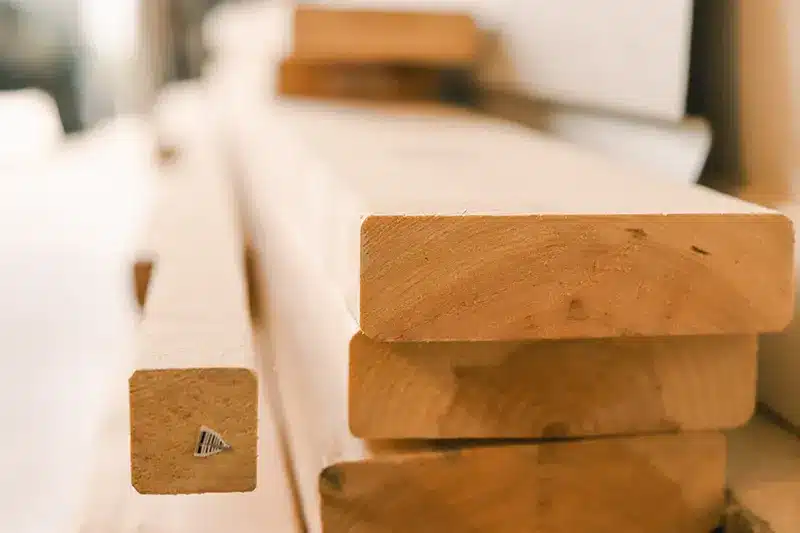
Traditional timber framing techniques or engineered wood materials, such as laminated veneer lumber or cross-laminated timber, may be used to build prefabricated wooden homes.
Steel: Steel is another popular material for prefab and modular houses due to its strength, durability, and fire resistance.
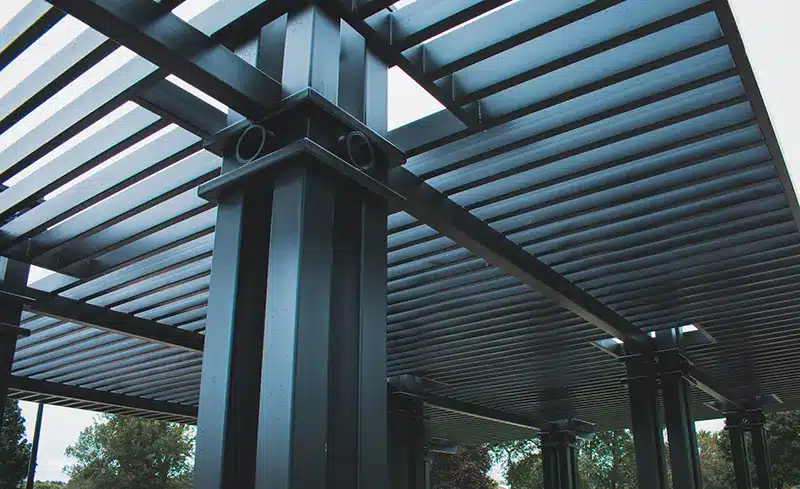
Steel frames and panels can be transported to the building site for assembly.
Concrete: Prefab homes are often built from robust, fire-resistant material concrete.
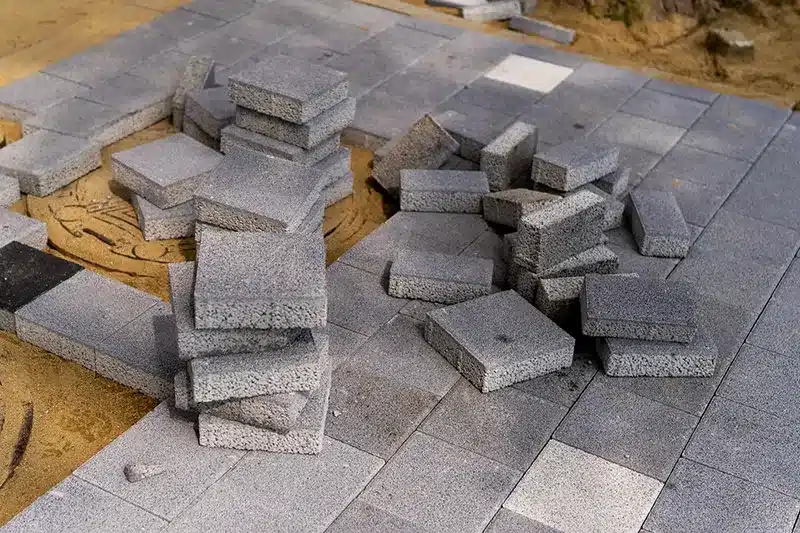
It may be shaped into a concrete block or panel, which can then be transported to the construction site and assembled there.
Prefabricated Panels: Prefabricated panels often comprise structural insulated panels like mineral wool, polyurethane, or expanded polystyrene.
These panels are produced off-site in a factory or manufacturing facility and may be utilized for walls, roofs, and floors.
Composites: Composite materials, like fiberglass or carbon fiber-reinforced polymers, comprise two or more distinct components.
Composites are perfect for use in prefab homes and modular home buildings since they are sturdy, light, and fire and corrosion-resistant.
Prefab construction materials vary depending on the project’s needs and unique design.
The selection of materials must be carefully thought out throughout the design and building stages since it might affect the house’s longevity, energy efficiency, and total cost.
Comparison of the Durability of Materials Used in Prefab Houses
Material | Durability in Prefab Houses |
Wood | Can be durable if treated properly and maintained regularly. Susceptible to rot, insects, and fire. |
Steel | Highly durable and strong. Resistant to weather, pests, and fire. |
Concrete | Highly durable and strong. Resistant to weather, pests, and fire. |
Prefabricated Panels | Can be highly durable if made of good materials and properly installed. Susceptible to damage during transportation. |
Composite | Highly durable, lightweight, and resistant to corrosion and fire. |
It’s vital to remember that the longevity of any material will rely on elements like quality, upkeep, and usage.
Prefabricated materials are, however, often produced to higher quality standards and put through thorough testing before being utilized in construction.
Because of this, they may be more durable than conventional building materials, which could have irregularities during the on-site installation.
Construction and Design of Prefabricated Houses
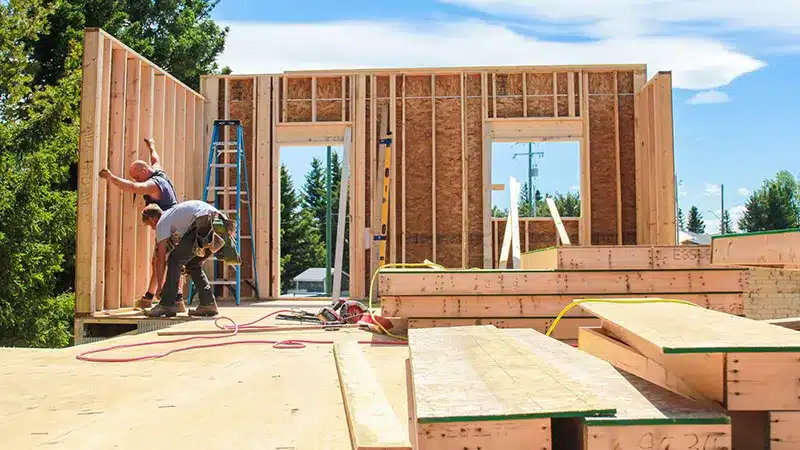
Prefabricated homes are created and constructed off-site in a factory or manufacturing facility before being delivered to the site and put together.
The main phases of the process may be broken down into the following:
1. Design: The evaluation of the needs and requirements of the customer initiates the design process.
Architects and designers then develop the house’s plan utilizing computer-aided design (CAD) software. Before production gets started, the client reviews and approves the design.
2. Manufacturing: When the design has been completed, the production process may start.
The home is built in portions or modules using the selected materials and manufacturing methods. The construction site is then visited to assemble these parts.
3. Transportation: The prefabricated sections are transported to the building site using flatbed trucks or specialized vehicles.
Meticulous planning is required to ensure that the sections are delivered in the correct order and sequence.
4. Assembly: On-site assembly typically takes time, depending on the complexity of the design.
The prefabricated sections are fitted together and secured, and finishing touches such as plumbing and electrical systems are installed.
How design and construction affect the durability of prefab houses
The design and construction influence the longevity of prefab or manufactured homes. Hereunder are some crucial factors to think about.
Materials: A prefab house’s longevity may be impacted by the choice of materials.
The home may survive for a long time if constructed with high-quality materials resistant to the elements, pests, and fire.
Structural integrity: The house must be designed to withstand the stresses and strains of transportation and assembly.
Properly engineered structures and connections can help ensure the house is structurally sound and durable.
Maintenance: Regular maintenance and upkeep are essential to ensure the house remains in good condition over time, which includes tasks such as painting, sealing, and cleaning.
Quality control: Quality control (QC) is a critical aspect of prefab house manufacturing.
QC measures ensure that each house component meets the required standards. This helps ensure consistency in the finished product. Poor-quality components can compromise the house’s and its occupants’ safety.
Modular home manufacturers can ensure that their materials satisfy the requirements and expectations of their customers and last the test of time by investing in quality control procedures.
Factors that Affect the Durability of Prefabricated Houses
Prefab houses are known for their durability, but numerous factors can impact their longevity.
Weather and Climate Conditions
The resilience of a prefab home may be significantly impacted by weather and climatic conditions.
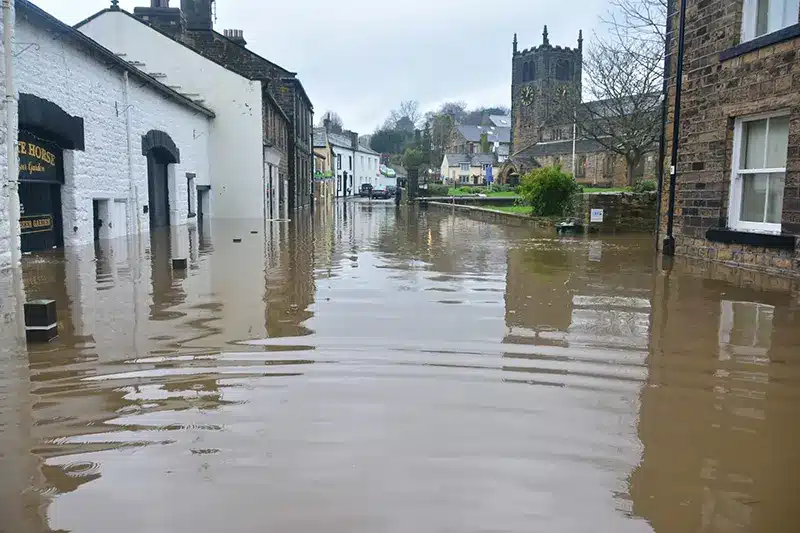
Extreme weather conditions may deteriorate the building’s materials and create wear and tear.
Using materials to survive these circumstances and maintaining the home is crucial to lessen these consequences.
Location and Site-Specific Factors
The location and site-specific factors can also affect the durability of a prefabricated house.
Factors such as soil type, water table, and slope can impact the stability of the permanent foundation and the overall structure.
Proper site preparation and foundation design are essential to ensure the house is built to last.
Maintenance and Upkeep
Regular maintenance and upkeep are critical to the durability of a prefabricated house.
This task includes cleaning gutters, inspecting the roof, and sealing windows and doors. Neglecting maintenance tasks can lead to damage and deterioration of the house.
Quality of Materials
Another critical aspect of a prefabricated house’s endurance is the caliber of the materials utilized in its construction process.
The home may survive for a long time if constructed with good materials resistant to fire, vermin, and the elements.
It is crucial to ensure the materials are placed correctly and chosen according to the climate and location of the property.
Maintenance and Repair of Prefabricated Houses
Prefab houses are known for their durability and low maintenance requirements.
However, regular maintenance is essential to ensure the house remains in good condition and lasts many years.
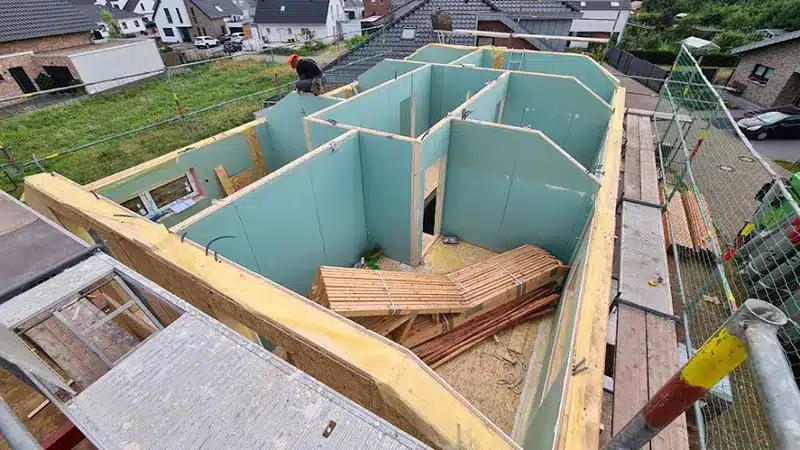
Regularly maintaining prefab houses is essential to prevent minor issues from becoming major problems. Some essential maintenance tasks include:
- Cleaning gutters and drains to prevent water damage
- Inspecting and repairing the roof to prevent leaks
- Checking windows and doors for air leaks and sealing them as necessary
- Checking the foundation and repairing any cracks or damage
- Maintaining HVAC systems
- Inspecting and maintaining plumbing and electrical systems
The manufacturer’s recommendations, or at least once a year, should be followed during these maintenance procedures.
Although householders may do specific simple maintenance jobs and repairs, more complicated jobs must be left to specialists.
For instance, a qualified expert should handle maintenance and repairs on HVAC systems, and a certified electrician should handle electrical work.
Conclusion
Prefabricated homes are solid and resistant to many of the same things that conventional homes can.
They have many benefits over traditional construction methods, including quicker construction timeframes, lower costs, and greater energy efficiency.
Nevertheless, the elements mentioned above may affect how long prefabricated homes last.
Working with a trustworthy general contractor is crucial, as are regular upkeep and prompt repairs and using quality materials suitable for the climate and location of the home.