So you’ve got yourself a shipping container, and now you’re itching to convert it into a full-fledged living space, workshop, or storage area. The first thing on your checklist? Insulation. But how much is that going to set you back?
Shipping container insulation cost varies widely, depending on factors such as the insulation material chosen, the size of the container, and labor rates in your area. On average, you could spend anywhere from $1,500 to $5,000 on insulating a standard 20-foot container.
Stick around as we delve into all the nuances of shipping container insulation costs, from type-specific costs to location-based variables. Let’s get you prepared, shall we?
Why Insulation is Crucial for Shipping Containers
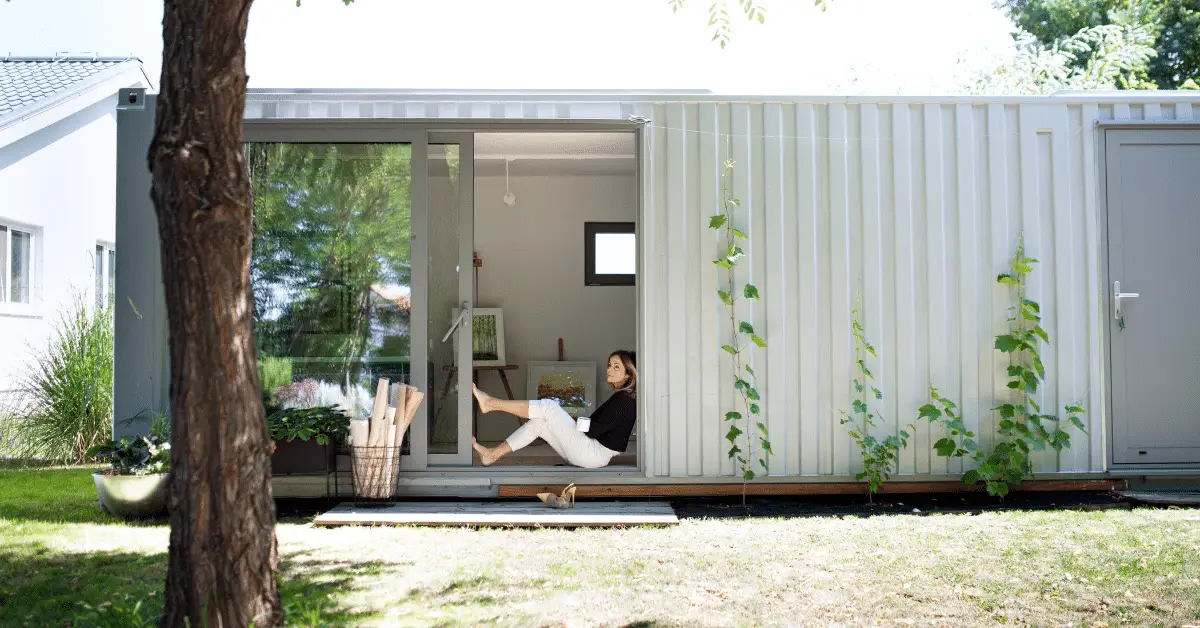
So, you’re probably asking, “Do I really need to insulate my shipping container?” The short answer is a resounding yes. Let’s dive into why insulation is more than just a comfort feature; it’s a necessity.
Climate Control: The Basics
Insulation is the first step in achieving a comfortable internal climate, especially if you are in the process of building a shipping container home. Without proper insulation, you’d be subjecting yourself to unbearable heat during the summer and freezing temperatures in winter. Consider that a steel box can quickly become an oven or an icebox depending on the season. Moreover, insulation can also help control humidity, which is essential for preventing mold and other moisture-related problems.
Protecting Your Valuables: Why Insulation Matters
When you use the shipping container for storage, proper insulation will protect your valuables from extreme temperature fluctuations, which can ruin delicate items like electronics and perishable food supplies. Even more resilient items like tools or furniture can suffer from corrosion or warping due to moisture that comes with temperature changes. In addition to temperature control, proper insulation can also keep out pests that might otherwise find a way into an improperly sealed container.
Energy Efficiency: Long-Term Benefits
Insulation isn’t just about immediate comfort or item preservation; it’s also about long-term energy efficiency. By maintaining a steady internal temperature, you’re less reliant on heating or cooling systems. This energy efficiency is not just about reducing costs; it’s also about reducing your environmental impact. Over the years, these savings can add up to a substantial amount, effectively paying back the initial investment you made on insulation.
Factors Affecting Shipping Container Insulation Cost
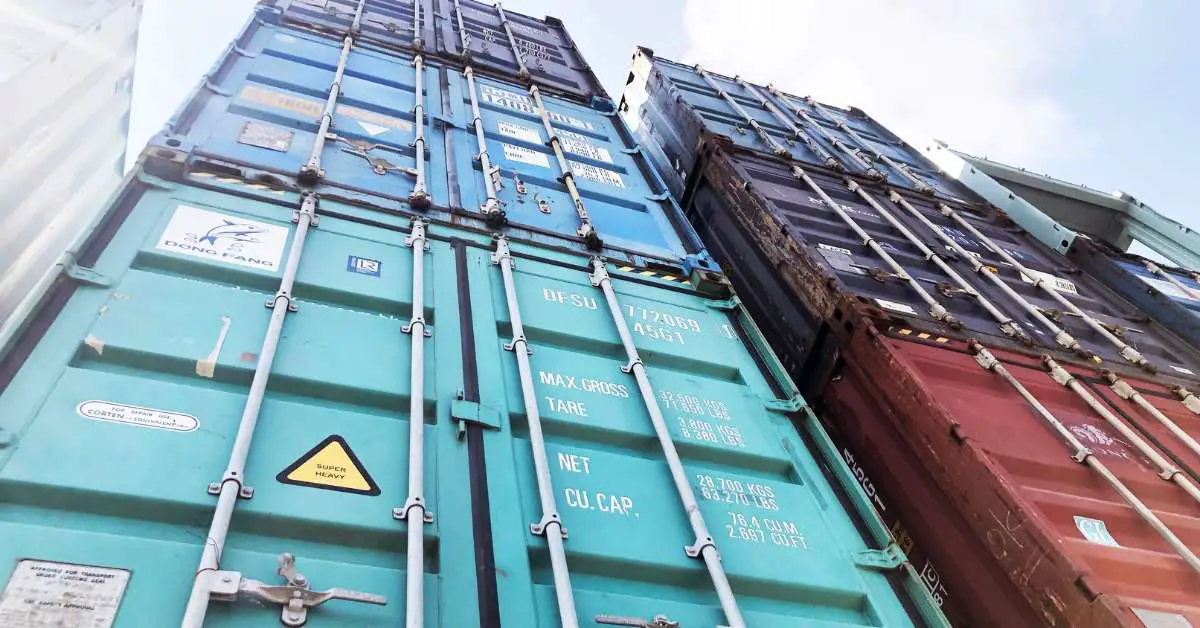
Alright, you get it: insulation is important. But how much is it going to cost you? Let’s break down the factors that can influence the overall cost of insulating your shipping container.
Size of the Shipping Container
The size of the container you’re insulating is a direct factor in the cost. A 20-foot container might cost considerably less to insulate than a 40-foot one. Larger containers require more materials and can also be more labor-intensive, extending the timeframe of the project. If you’re considering insulating multiple containers, you should also think about whether they’ll be stacked or aligned, as this could affect the amount of insulation needed.
Type of Insulation Material
There are various types of insulation materials, each with its own set of pros and cons, not to mention varying costs. While spray foam might offer the best insulation, it’s often more expensive than foam boards or fiberglass. When choosing the type of insulation, you should also consider the R-value, which is a measure of thermal resistance. Higher R-values mean better insulating capabilities but often come at a higher price point.
Geographical Location and Labor Costs
Labor costs can be a significant chunk of your insulation budget and can vary wildly depending on your geographical location. In metropolitan areas, you’ll generally pay more for labor compared to rural regions. However, higher labor costs might be offset by easier access to materials, potentially saving you money on shipping and delivery. The local climate might also necessitate specific types of insulation materials that are more effective but also more expensive.
Building Codes and Regulations
Local and national building codes can have a significant impact on your insulation project. These codes might dictate the minimum R-value of insulation you need, as well as other safety features like fire resistance. Ignoring these requirements can lead to legal complications, including fines, or even necessitate redoing the work. Always consult local building codes or a professional to ensure that your insulation meets the necessary standards.
Types of Insulation Materials and Their Costs
By now, you should have a decent grasp of the variables affecting your insulation costs. Next, let’s explore the types of insulation materials you can choose from and their relative costs.
Spray Foam Insulation: Pros and Cons
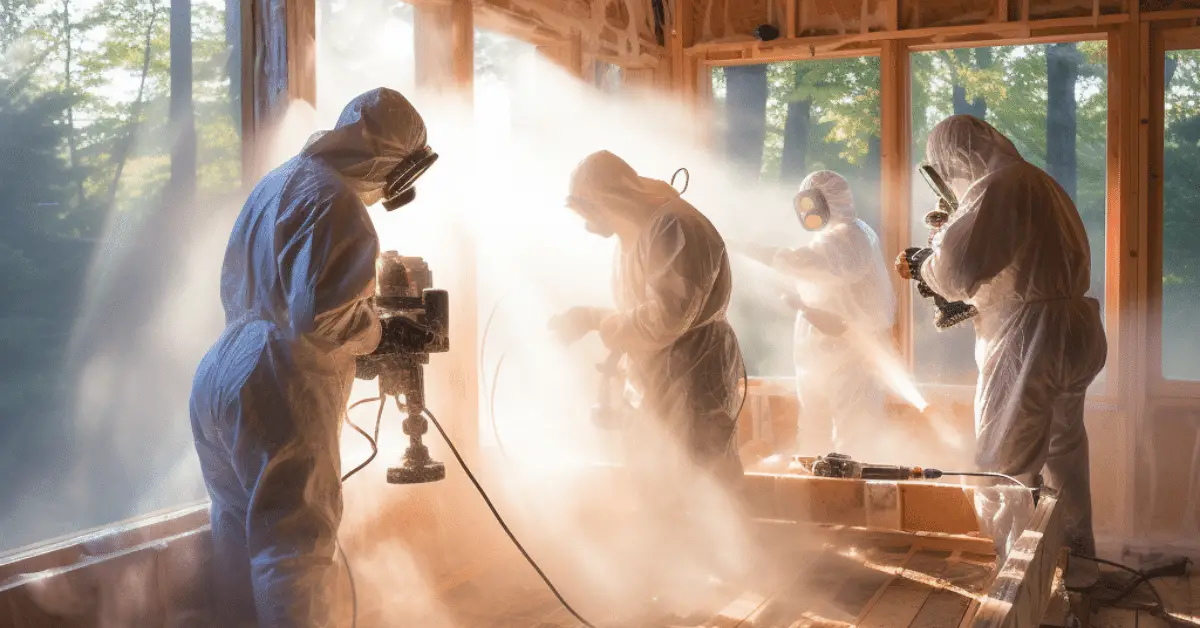
Spray foam insulation is the go-to for superior thermal resistance. It provides an air-tight seal and is highly effective at keeping the interior temperature stable. Cost-wise, you’re looking at around $2.00 to $3.00 per square foot, making it one of the more expensive options out there.
On the flip side, installing spray foam usually requires a professional touch due to the equipment involved and the need for precision application. If not installed correctly, spray foam can develop gaps or inconsistencies that compromise its effectiveness. So while it offers top-notch insulation, the higher costs and need for professional installation are points to consider carefully.
Foam Boards: An Overview
Foam boards are a more budget-friendly alternative, costing between $1.00 to $1.50 per square foot. They offer solid insulation performance and are generally easier to install, which could save you on labor expenses.
However, foam boards have their limitations. They don’t always provide as comprehensive coverage as spray foam, leaving potential gaps where heat or cold can escape. Additionally, you may need to install a fire-retardant layer or a vapor barrier, adding to your overall costs.
Fiberglass: What You Need to Know
Fiberglass is a classic choice for insulation, especially if you’re watching your budget. It usually costs between $0.50 to $1.00 per square foot and is relatively straightforward to install. It offers good, though not exceptional, thermal resistance, making it a solid choice for moderate climates.
Despite its affordability and ease of installation, fiberglass has its downsides. It’s less effective in extreme temperatures, and you’ll likely need a vapor barrier or fire-resistant layers. Also, proper protective gear is essential during installation to prevent skin irritation or respiratory issues.
Alternative and Recycled Materials
If you’re eco-conscious, alternative materials like recycled denim or sheep’s wool may be appealing. These materials tend to cost around $1.20 to $2.00 per square foot. They’re less traditional but provide a more sustainable option for insulation.
While you might love the idea of using recycled or alternative materials, be aware that they often have a lower R-value. This means you may need thicker layers to achieve comparable insulation, which could affect your interior space and overall costs.
Cost Calculations: What You Can Expect to Pay
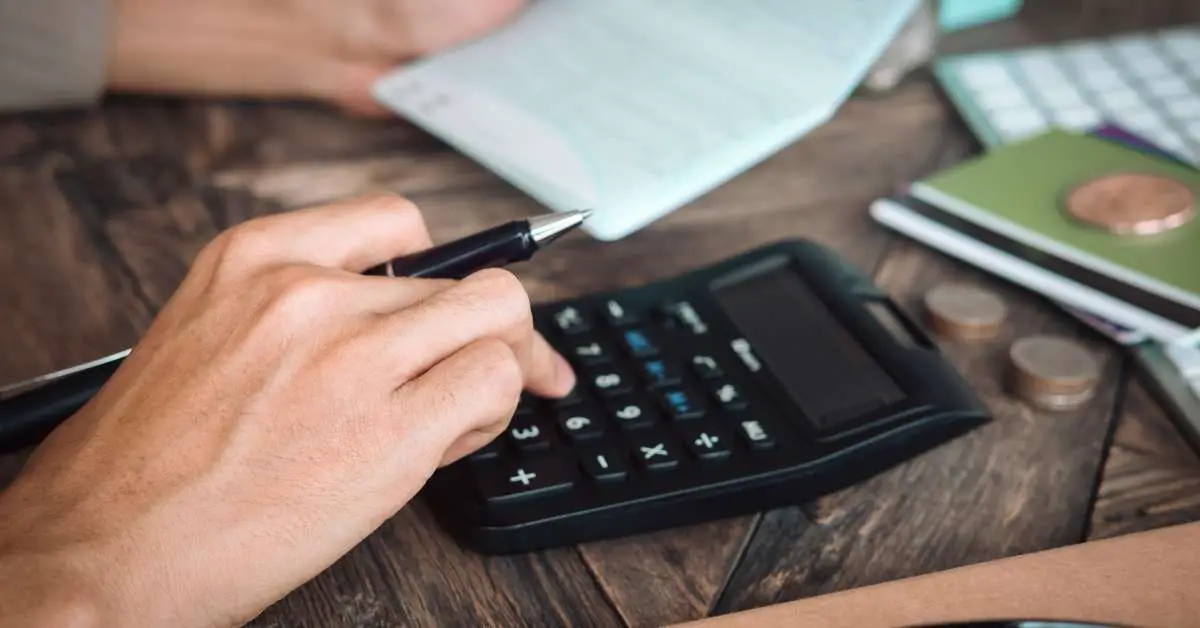
You’re getting closer to making an informed decision. But let’s get down to brass tacks: how much are you actually going to pay for your shipping container insulation?
Per Square Foot Calculations
Starting with a per-square-foot calculation can offer a ballpark figure, giving you a tangible basis for your budget. For example, spray foam costs around $2.00 to $3.00 per square foot. If you have a 320-square-foot container, you could be looking at a total cost ranging from $640 to $960.
This per-square-foot approach can be particularly useful for comparison shopping. Whether you’re looking at different material types or considering multiple vendors, this calculation gives you an apples-to-apples comparison to gauge your options.
Bulk Purchasing and Discounts
Buying in bulk is a tried-and-true way to save money, and insulation is no exception. If you’re planning to insulate multiple shipping containers, you may be able to secure a discount that drops your per-square-foot cost by 10-20%.
When you’re at this stage, clear communication with suppliers is crucial. Ask about volume discounts, seasonal promotions, or any special deals they might have running. It never hurts to ask, and you could land some significant savings.
DIY vs. Professional Installation
Installing the insulation yourself can save you money, particularly on labor costs, which can range from $1.00 to $3.00 per square foot. However, be realistic about your DIY skills and the complexity of the material you’re using.
While DIY can save money upfront, remember to factor in the potential costs of mistakes or inadequate installation. Time, effort, and any do-overs should be considered when deciding between DIY and professional installation. Evaluate your comfort level with the installation process and weigh it against the potential savings to make the right choice for you.
Hidden Costs and Additional Expenses
Just when you thought you had it all figured out, remember there can be hidden costs. Don’t let these surprise expenses catch you off guard.
Vapor Barriers and Interior Paneling
Some types of insulation like fiberglass may require additional vapor barriers or interior paneling, costing around $0.50 to $1.00 extra per square foot. These add-ons are crucial for preventing moisture buildup but can add unexpected costs to your project.
Fire-Resistant Upgrades
If your local building codes require it, or you’re storing sensitive materials, fire-resistant insulation may be necessary. Fire-resistant options can cost an additional $0.50 to $1.00 per square foot, depending on the type of insulation you choose.
Seasonal Price Fluctuations
Believe it or not, the costs of materials and labor can fluctuate based on the season. Offseason projects could save you as much as 15-20% in costs. Timing your project right can lead to substantial savings, so keep an eye on market trends.
How Location Affects Insulation Costs
You might not realize it, but where you’re located can greatly influence your insulation needs and, by extension, costs. Let’s explore how.
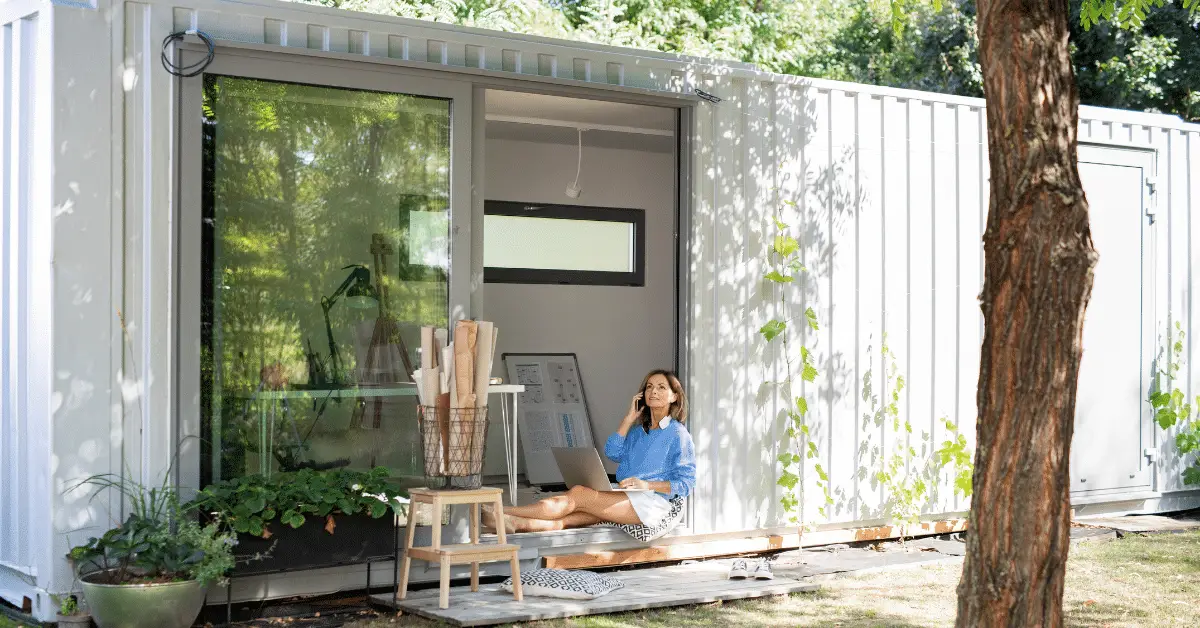
Regional Price Variations
Prices for container homes, insulation materials, and labor can differ significantly depending on your location. For instance, you may find that costs are higher in big cities compared to rural areas due to the increased demand and cost of living. To get an accurate gauge, it’s advisable to seek out local quotes and factor them into your budget.
Moreover, availability of certain materials might also be region-dependent. A material that is readily available in one region could be scarce and expensive in another, further affecting costs. It’s a good idea to do local market research to see what materials are both effective and economical for your specific location.
Climate-Specific Insulation Needs
Different climates necessitate different insulation solutions. Hot, humid climates may require moisture- and mold-resistant insulation materials, which generally come at a premium. On the other hand, colder climates may necessitate higher R-values, leading to thicker or more specialized insulation.
If you’re in an area prone to extreme weather conditions, like heavy snowfall or intense heat, you may need to invest in insulation that is resilient to such conditions. For example, certain insulation types are better at not only retaining heat but also at wicking away moisture, which can be a crucial factor in maintaining the integrity of the container and its contents.
Local Building Codes and Permits
When planning your insulation project, don’t overlook local building codes and permit requirements. These can stipulate the types of materials you can use and the installation methods you must adhere to. Ignoring these can result in hefty fines or, worse, the complete redoing of your insulation work.
Additionally, different municipalities may offer incentives for using certain environmentally-friendly insulation materials. So, while adhering to local regulations might seem burdensome, it can also provide opportunities for cost savings and environmental stewardship.
Financial Benefits of Quality Insulation
Investing in insulation isn’t just a short-term expense; it can actually save you money in the long run.
Long-Term Energy Savings
Quality insulation materials will be more efficient at temperature regulation, which can significantly reduce your reliance on external heating or cooling systems. This means you can expect a decrease in your energy bills over the long term.
Besides just the monthly savings on utility bills, you’re also extending the lifespan of your heating and cooling units by reducing their workload. This could result in less frequent repairs and replacements, offering additional long-term savings.
Possible Tax Credits and Rebates
Various federal, state, or local programs offer tax credits and rebates for installing energy-efficient insulation. These incentives can offset a portion of your upfront costs, making quality insulation more affordable than it initially seems.
However, to qualify for these benefits, your insulation material and installation method often have to meet specific criteria. Always check the requirements in your jurisdiction and make sure to keep all relevant documentation, as you may need to provide these during the tax filing process.
Increased Property Value
Quality insulation can significantly increase the value of your shipping container. This is especially beneficial if you ever decide to sell or rent it out, as well-insulated containers are more attractive to potential buyers or tenants.
Moreover, a well-insulated container is a sign of a well-maintained property, which can add credibility and reliability in the eyes of prospective buyers or renters. As such, your initial investment in quality insulation could yield higher financial returns in the long run.
Tips for Budgeting Your Shipping Container Insulation
We’re almost at the finish line! Before you start your insulation project, let’s discuss some last-minute budgeting tips.
Obtaining Accurate Estimates
It’s essential to collect multiple estimates from various suppliers and installers before starting your project. This can help you understand the market rates better and allows for more accurate budgeting. Estimates should include not just the cost of materials but also labor, transportation, and any additional items like vapor barriers.
In addition to comparing prices, also consider the reputation and reliability of the suppliers and installers. Cheaper isn’t always better, especially if it compromises the quality of your insulation. Look for customer reviews or ask for references to make an informed decision.
When to Invest in High-Quality Materials
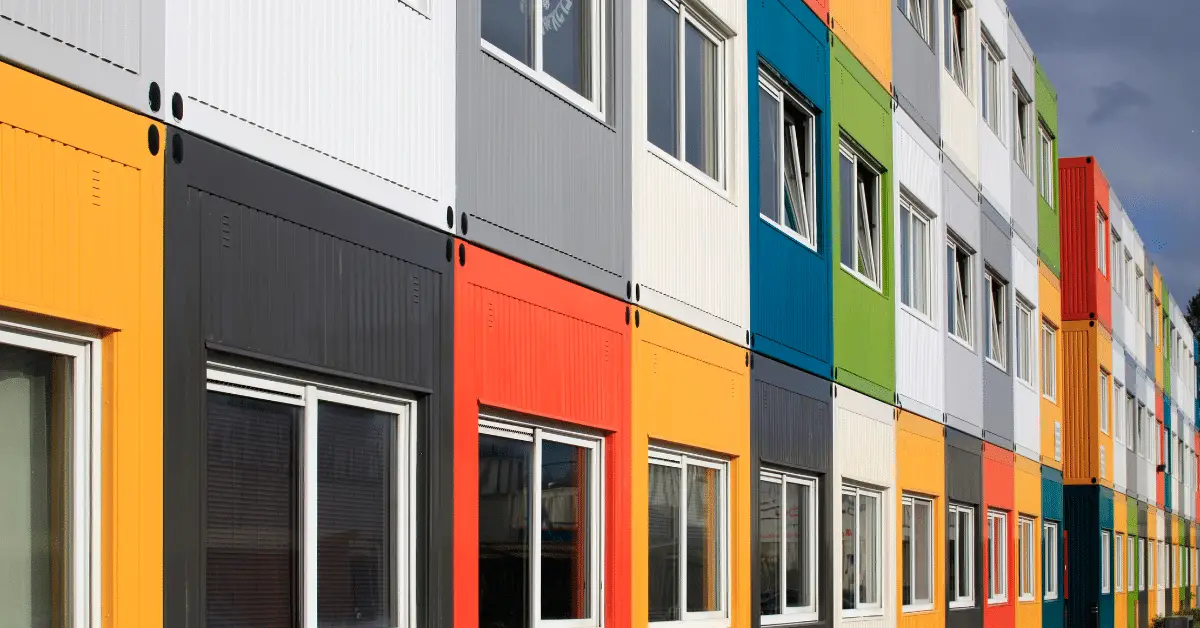
If your shipping container will serve as a long-term residence or for storing valuable items, investing in higher-quality insulation materials is advisable. Better materials usually offer superior performance, durability, and may come with extended warranties.
Moreover, in conditions where temperature and humidity control is crucial—like in living spaces or for storing sensitive items—high-quality insulation can provide the consistent environment you need. In such cases, spending a bit more upfront can save you money and hassle in the long run.
Bundling Costs: Part of a Larger Project
If your insulation needs are part of a larger renovation or conversion project for your shipping container, you may be able to bundle services for a discount. Many contractors offer package deals for multiple services, which could bring down your overall costs.
However, ensure that bundling doesn’t compromise the quality of the work. Each aspect of your project, including insulation, requires expertise and attention to detail. Safety issues may arise if quality is compromised. Before agreeing to a package deal, clarify what it entails and whether it meets all your specific needs and complies with local regulations.
Making Smart Choices in Shipping Container Insulation
You’ve been through the wringer, absorbing everything there is to know about shipping container insulation costs. From understanding why insulation is a must to navigating the myriad of choices available, you’re now equipped to make an informed decision.
So go ahead, start that insulation project with confidence. Whether you’re a prepper building a sustainable living space or someone just looking for secure storage, insulation is a worthwhile investment that will pay off in comfort, energy savings, and peace of mind.