Some acronyms in polymers and chemical compounds often lead to confusion. TFE and PTFE are no exceptions. These two substances might appear interchangeable at first glance. But are they the same, or do their unique properties set them apart?
TFE and PTFE are not the same thing but are closely related. TFE, or Tetrafluoroethylene, is a monomer used in the production of PTFE, or Polytetrafluoroethylene. PTFE is a fluoropolymer known for its non-stick properties, while TFE is the basic building block to make PTFE.
Let’s dive deeper into understanding these fascinating materials: their properties, applications, and any potential hazards of handling them safely in your lab or workplace environment.
What is TFE?
TFE, or Tetrafluoroethylene, is a highly versatile fluoropolymer with exceptional chemical and physical properties. It is often confused with PTFE or polytetrafluoroethylene, a specific type of TFE polymer.
Chemical and Physical Properties
Tetrafluoroethylene, commonly known as TFE, is a remarkable chemical compound that plays a pivotal role in materials science. Its molecular structure consists of four fluorine atoms symmetrically bonded to two carbon atoms. This unique arrangement grants TFE a range of extraordinary properties and potential applications.
Its strong carbon-fluorine bonds define TFE’s chemical structure, making it incredibly stable and resistant to chemical reactions. This stability arises from the fluorine atoms’ strong electronegativity.
TFE exhibits several intriguing physical properties. It is a colorless and odorless gas at room temperature and pressure, making it an unassuming yet powerful substance. Its low surface energy imparts non-stick characteristics, while its resistance to extreme temperatures and most chemicals is remarkable.
TFE is non-conductive, making it ideal for applications involving electrical insulation.
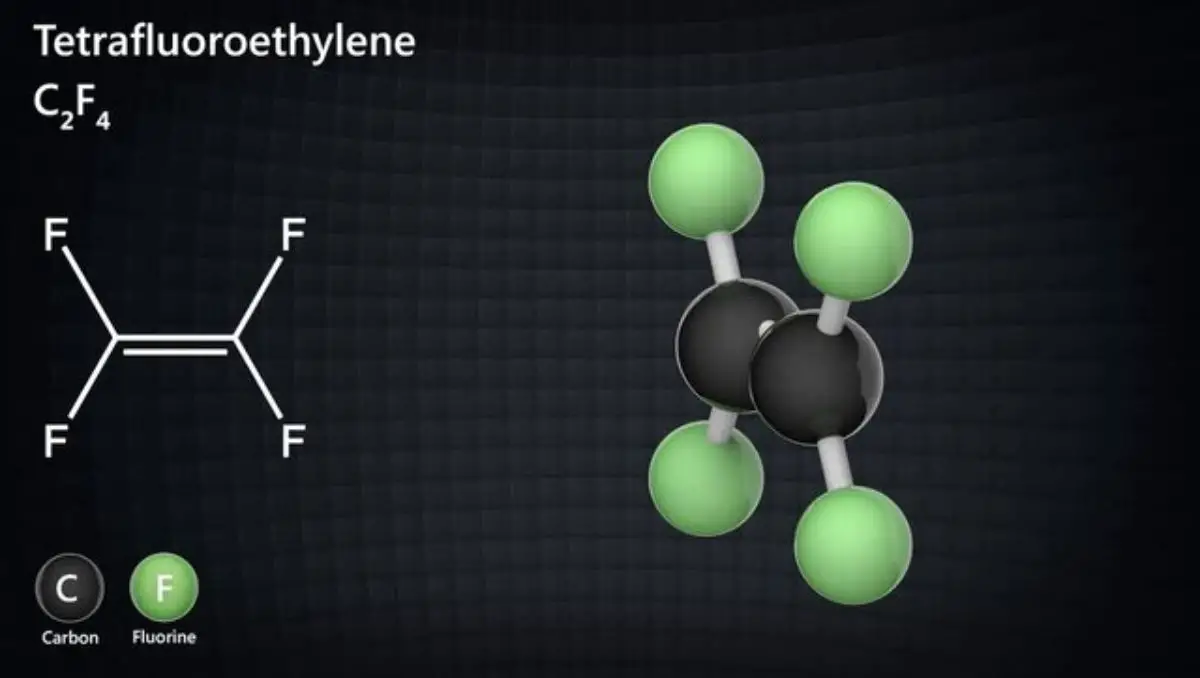
Production and Manufacturing Process
The production and manufacturing process of TFE involves several crucial steps to obtain this critical chemical compound. The process starts with acquiring the primary raw material, chlorodifluoromethane, also known as HCFC-22, a chlorofluorocarbon (CFC) compound.
HCFC-22 can be sourced from various methods, including the reclamation of CFCs or hydrochlorofluorocarbon (HCFC) feedstock. The core of TFE production lies in the pyrolysis of HCFC-22, conducted in a controlled environment.
Typically, this process involves high-temperature treatment, often with a catalyst or electric discharge methods. The purified TFE then undergoes further purification processes, including distillation and scrubbing, to remove impurities, ensuring the desired purity level.
This purified TFE serves as the primary feedstock for producing Polytetrafluoroethylene (PTFE), a widely used material known for its non-stick properties, chemical inertness, and high-temperature resistance.
Uses and Applications
Due to its unique chemical properties, TFE finds application in several important areas. Some of its primary uses and applications include:
- PTFE production
- Industrial lubricants
- High-performance seals
- Electrical insulation
- Chemical processing
- Coatings and linings
- Valve components
- Aerospace
- Pharmaceutical and medical devices
- Automotive industry
Safety Considerations
Safety is paramount when dealing with TFE due to its unique chemical properties and potential hazards. TFE is a hazardous gas that should only be handled in well-ventilated areas or under exhaust hoods to prevent the accumulation of potentially harmful TFE vapors.
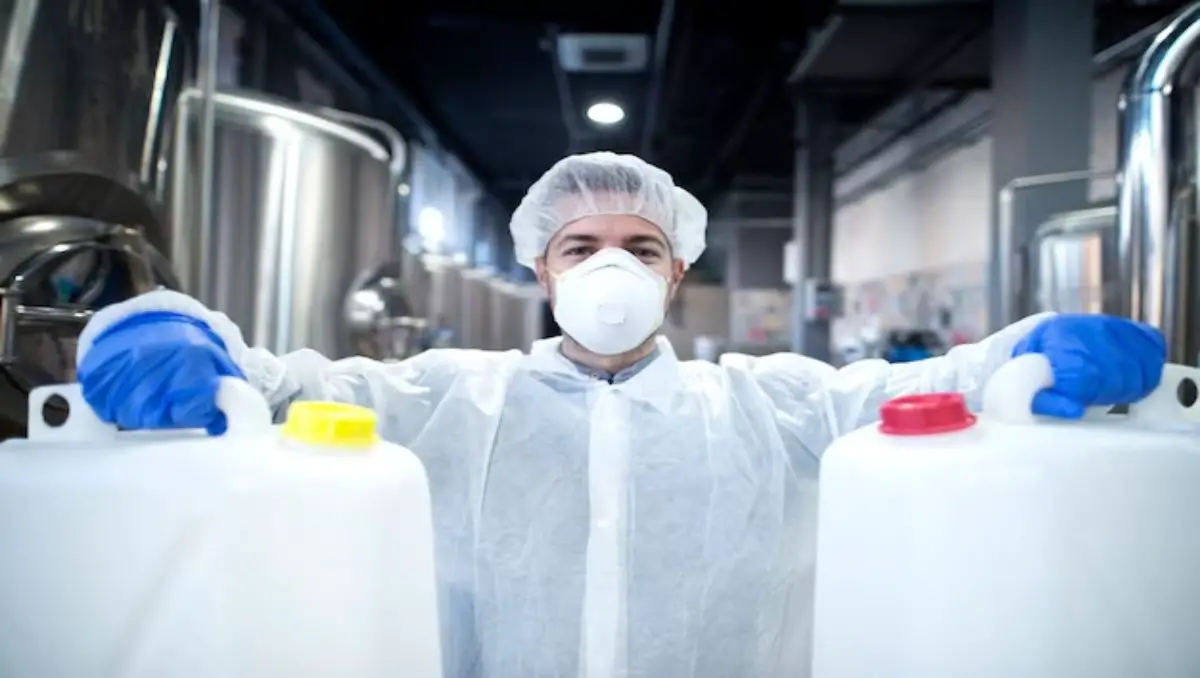
Proper personal protective equipment (PPE), including chemical-resistant gloves, safety goggles, and, in some cases, respirators, is essential when working with TFE to protect against inhalation and contact with the skin or eyes. Emergency response plans and equipment, such as safety showers, eyewash stations, and fire suppression systems, should be readily available to respond swiftly in case of accidents or leaks.
Personnel handling TFE must receive thorough training and education on its safe use, including understanding the associated hazards and the proper storage and disposal procedures. Regular monitoring and leak detection systems are essential to promptly identify and mitigate any leaks or releases.
Although TFE is not flammable, it can decompose at high temperatures, producing hazardous by-products. Facilities handling TFE should have fire safety measures in place to control potential fires and protect against the hazards associated with thermal decomposition. Proper storage of TFE is also critical.
Pros and Cons
Although there are advantages to using PTFE, there are also disadvantages that need to be considered.
Pros
- Chemical Stability: TFE’s exceptional chemical stability makes it invaluable in various applications.
- Low Friction: Its low friction properties reduce wear and tear in machinery and equipment.
- Electrical Insulation: TFE’s non-conductive nature is ideal for electrical insulation.
- Wide Temperature Range Usability: TFE remains stable across a broad temperature range, making it adaptable to diverse conditions.
Cons:
- Hazardous By-Products: The pyrolysis of TFE precursor compounds can produce hazardous by-products, requiring careful handling.
- Energy-Intensive Production: The production of TFE can be energy-intensive and costly.
- Limited Applications: TFE’s applications are primarily confined to the production of PTFE, limiting its versatility compared to its derivative.
What is PTFE?
PTFE, or Polytetrafluoroethylene, is a synthetic fluoropolymer of Tetrafluoroethylene. It has exceptional chemical and physical properties, making it highly resistant to heat, chemicals, and electrical conductivity. PTFE is produced through polymerization, where the monomer TFE is heated under pressure in the presence of a catalyst.
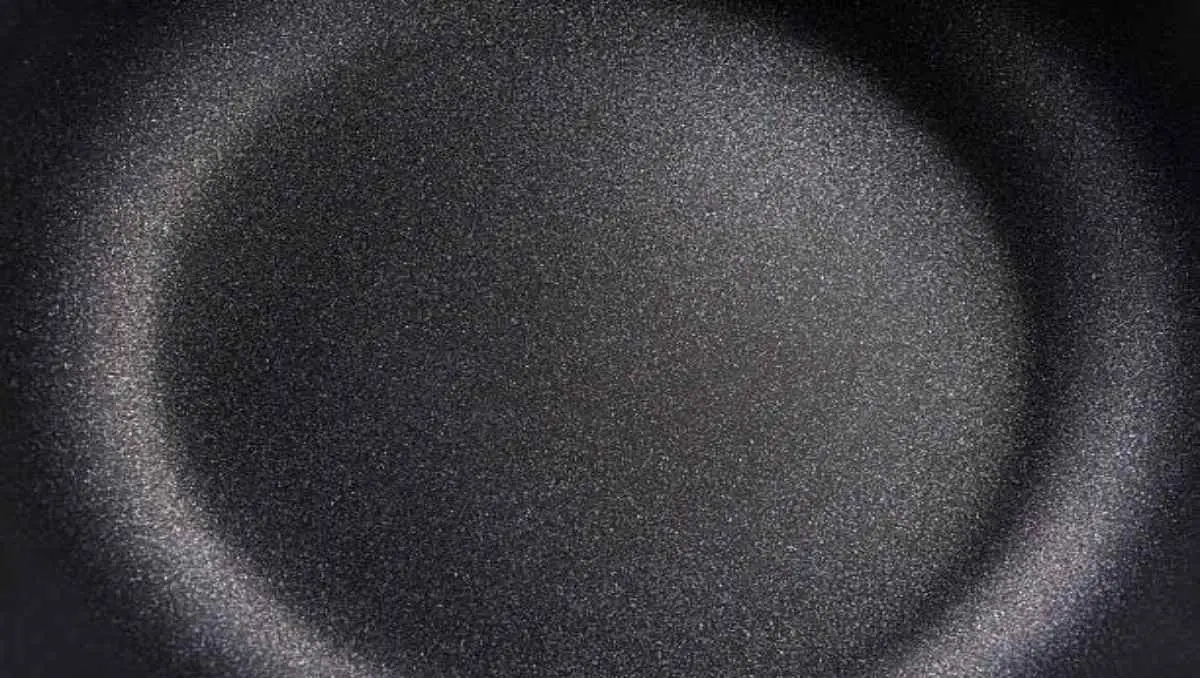
Chemical and Physical Properties
PTFE is a remarkable polymer renowned for its unique chemical and physical properties. Chemically, PTFE is a fluoropolymer composed of carbon and fluorine atoms, with the carbon atoms forming a chain-like structure. One of its most remarkable characteristics is its high degree of fluorination, resulting in a solid carbon-fluorine bond.
This strong bond imparts outstanding chemical stability to PTFE, making it highly resistant to chemical reactions, even in the presence of aggressive acids, bases, and solvents. This property is one of the primary reasons for PTFE’s widespread use in applications where corrosion resistance is crucial.
Physically, PTFE exhibits several remarkable properties. It is solid at room temperature and possesses a low coefficient of friction, giving it excellent non-stick qualities. This non-stick characteristic is particularly well-known in cookware, where PTFE coatings ensure food does not adhere to the surface, making it easy to clean and preventing sticking or burning.
Furthermore, PTFE is an excellent electrical insulator due to its low dielectric constant, high resistivity, and non-conductive nature. This makes it suitable for electrical and electronic applications, including wire and cable insulation.
Production and Manufacturing Process
The production and manufacturing process of PTFE is a multi-step procedure. It begins with the primary raw material, TFE, which serves as the monomeric building block for PTFE.
The first step involves the polymerization of TFE. In this process, TFE gas is subjected to high pressure and temperature conditions, typically in the presence of a free radical initiator, which initiates the polymerization reaction.
After polymerization, the PTFE resin is cooled and granulated into a powder or turned into a fine powder directly. This fine PTFE powder can manufacture various PTFE products through processes like compression molding, sintering, or paste extrusion.
PTFE manufacturing also adheres to strict safety and environmental regulations due to the potential hazards associated with its production, such as releasing toxic fumes if not adequately handled.
This comprehensive manufacturing process enables the creation of PTFE products used in various industries, including cookware, electrical insulation, and industrial applications, where its unique properties are highly valued.
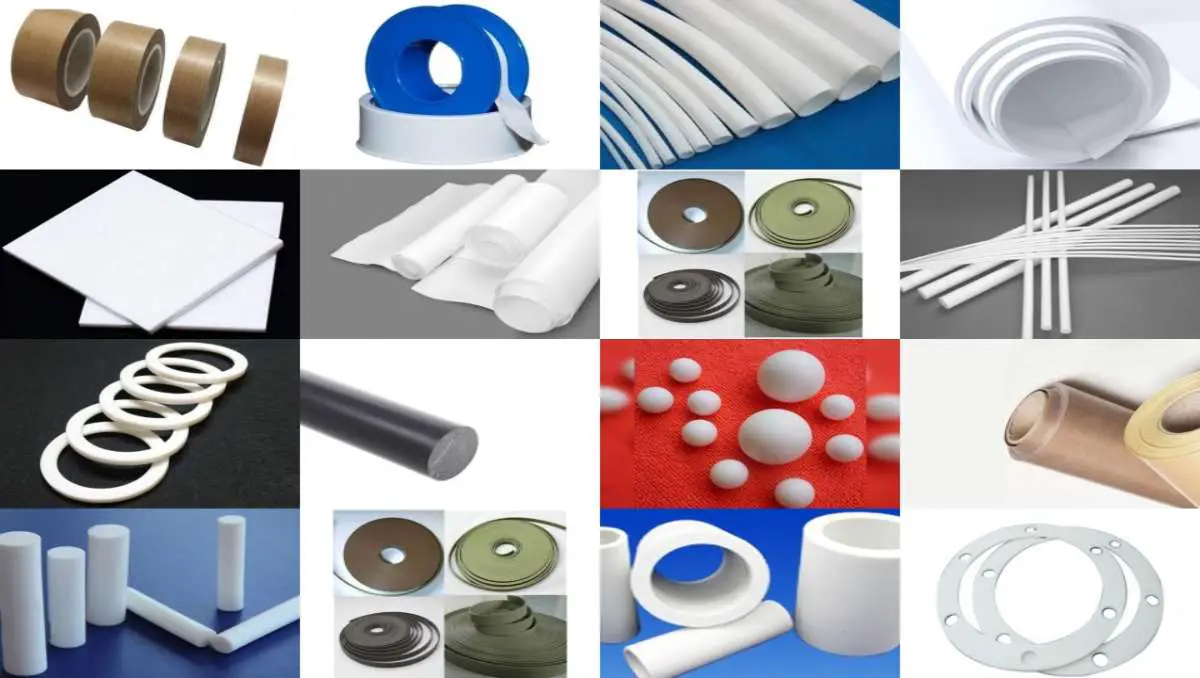
Uses and Applications
With its remarkable versatility and unrivaled performance, PTFE has entered countless industries. Here are some common uses and applications of PTFE:
- Non-stick coatings
- Seals and gaskets
- Bearings and bushings
- Electrical insulation
- Dry lubricant in various mechanisms
- Chemical containers
- Medical devices
- Aerospace
- O-rings
- Expansion joints
- Insulators
- Automotive components
- Pipe and tube liners
- Printers and copiers
- Chemical lab equipment
- Textile industry
- Slide bearings
- Conveyor belts and components used in food processing
- Valves, seals, and gaskets in the oil and gas sector
- Chemical pumps
Safety Considerations
One must be cautious when working with PTFE due to the potential release of toxic fumes if overheated. PTFE has excellent fire resistance properties, making it a preferred choice in applications with high temperatures.
However, it is essential to note that when PTFE is heated above its recommended temperature range (260-327°C), it can start to decompose and release toxic gases, including fluorocarbon compounds. These fumes can be harmful if inhaled and may cause flu-like symptoms or even more severe health effects.
To mitigate these toxicity concerns, safe handling procedures should always be followed when working with PTFE. This includes using adequate ventilation systems and personal protective equipment such as gloves and masks. Caution should be exercised to prevent overheating or burning of PTFE materials.
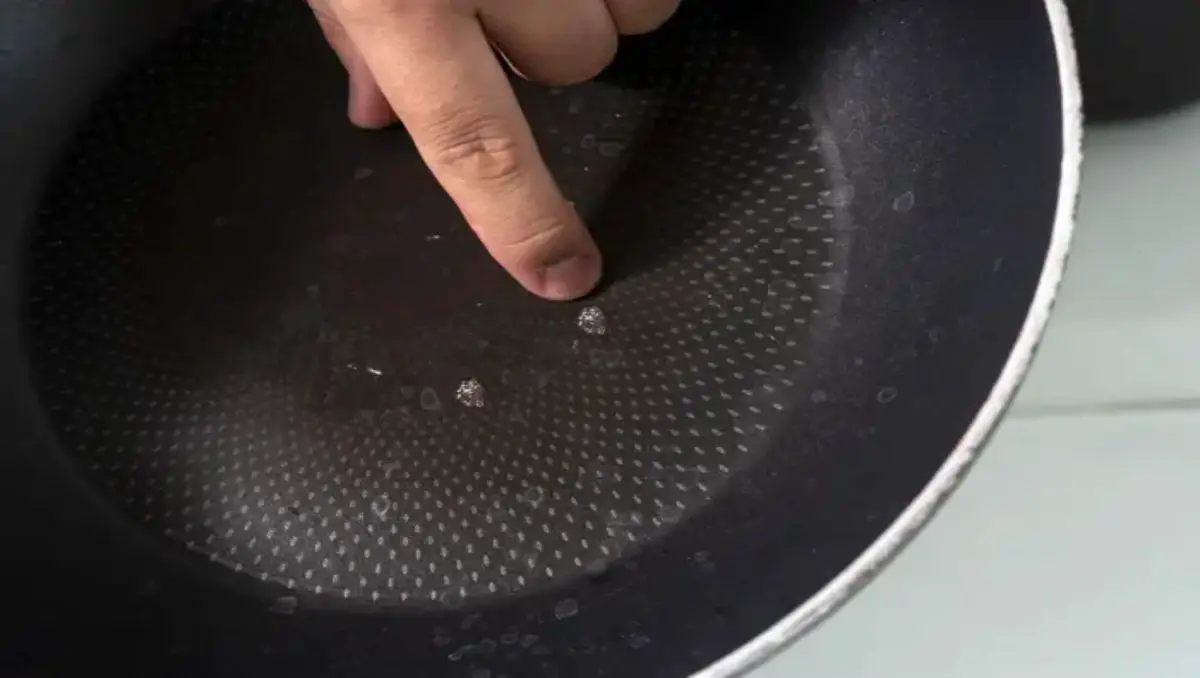
In terms of environmental impact, PTFE is considered relatively inert and does not readily degrade in the environment. However, the production process of PTFE involves the use of perfluorooctanoic acid (PFOA), which has been associated with environmental contamination concerns.
Pros and Cons
PTFE has numerous advantages and drawbacks that should be considered before using it in various applications.
Pros:
- Low Friction: PTFE has exceptionally low friction properties, making it an ideal choice for reducing friction in various applications.
- Chemical Resistance: PTFE is highly resistant to a wide range of chemicals and corrosive substances, making it suitable for use in harsh environments.
- Non-Stick Properties: Its non-stick surface is valuable for preventing adhesion in cookware and industrial applications.
- High-Temperature Stability: PTFE can withstand extreme temperatures, from -200°C to 260°C (-328°F to 500°F), without significant degradation, allowing it to perform in demanding heat conditions.
Cons:
- Cost: PTFE can be relatively expensive compared to other materials, which can limit its use in cost-sensitive applications.
- Limited Load-Bearing Capacity: PTFE is not as strong as some other materials, limiting its use in applications requiring high mechanical strength.
- Creep: Over time, PTFE can exhibit creep, which is the slow deformation under load, affecting long-term performance in some applications.
- Machinability: PTFE is challenging to machine due to its low friction coefficient, making fabrication and shaping more difficult than with some other materials.
So, Are TFE and PTFE The Same? Are There Any Differences?
In essence, TFE and PTFE are related but distinct compounds. The main differences between TFE and PTFE lie in their properties, production methods, and applications.
In terms of properties, TFE is a gas at room temperature, while PTFE is a solid with exceptional heat resistance. This makes PTFE more suitable for high-temperature applications. It exhibits excellent chemical resistance and a low friction coefficient, making it ideal for non-stick coatings.
When comparing the production methods of TFE and PTFE, it’s important to note that TFE is primarily produced through the polymerization of tetrafluoroethylene gas. On the other hand, PTFE is manufactured by free radical polymerization of tetrafluoroethylene in an aqueous medium.
PTFE finds extensive use due to its unique properties, such as electrical insulation, chemical inertness, and biocompatibility. It is commonly used in the automotive, medical devices, electronics, and cookware industries. Conversely, TFE has niche applications such as specialty chemicals or refrigerants used in air conditioning systems.
Here is a table that summarizes the key differences between TFE and PTFE:
Property | TFE | PTFE |
Chemical Formula | C2F4 | (C2F4)n |
State at Room Temperature | Gas | Solid |
Melting Point | -142.6 °C | 327 °C |
Boiling Point | -76.3 °C | N/A (decomposes before boiling) |
Solubility in Water | Insoluble | Insoluble |
Most Common Applications | PTFE, refrigerants, fire suppressants | Cookware, medical devices, industrial equipment, aerospace components, electrical insulation, textile coatings |
Although TFE and PTFE share similarities in composition and name initials (tetrafluoroethylene), they possess distinct characteristics that make them suitable for different purposes. Understanding these key differences can help determine which one best suits specific requirements.
How About Teflon?
Teflon is a brand name commonly associated with PTFE. PTFE is a synthetic polymer that was accidentally discovered in 1938 by a chemist named Roy Plunkett while working for the chemical company DuPont.
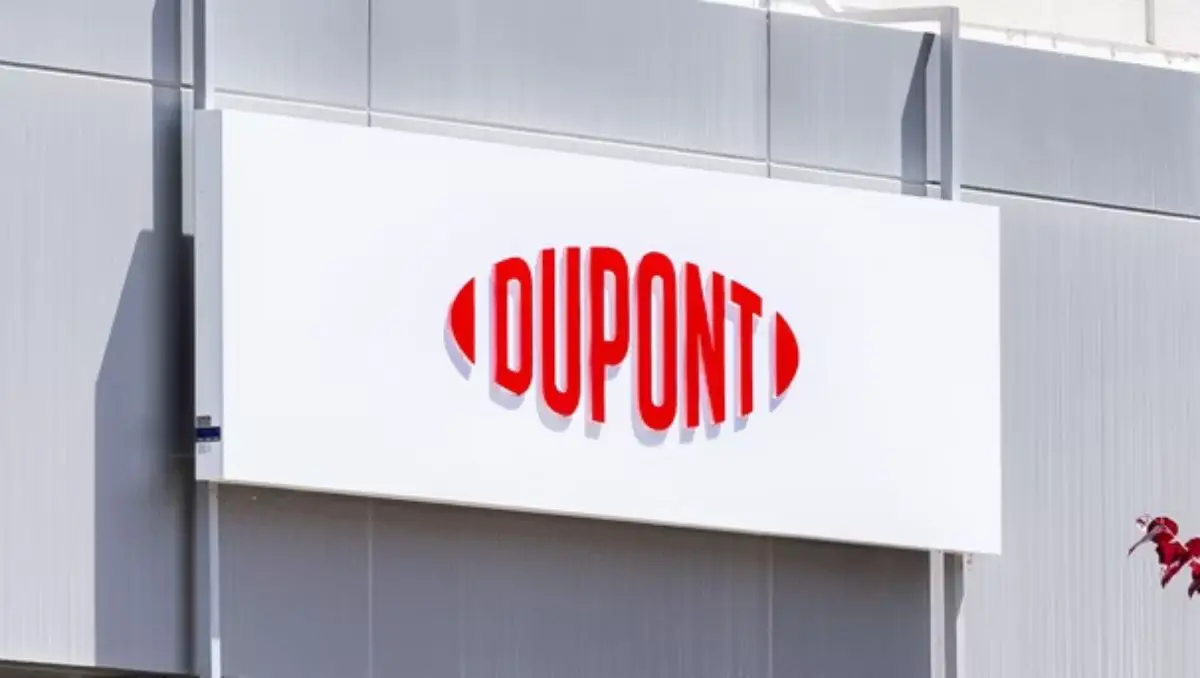
Plunkett was experimenting with refrigerants and stumbled upon the solid, waxy substance we now know as PTFE. DuPont later trademarked the material as Teflon.
Teflon and PTFE are often used interchangeably, but there is a distinction to be made. PTFE is the generic name for the polymer itself, whereas Teflon is a specific brand name owned by Chemours, a spin-off of DuPont.
Teflon is essentially a trade name for PTFE, much like Colgate is a brand of toothpaste. Teflon products are made from PTFE and are known for their remarkable non-stick properties, chemical resistance, and high-temperature stability. Many non-stick cookware, industrial coatings, and other applications use Teflon or PTFE materials.
On the other hand, if you’re looking for a non-stick alternative to Teflon, cast iron is a great option. Cast iron is naturally non-stick and doesn’t require any artificial coatings. Unlike Teflon, which can release harmful fumes when overheated, cast iron provides a safe and reliable cooking surface. It is also very durable and can last for generations, offering an excellent alternative without the concern of burnt Teflon.
TFE vs. PTFE: The Ultimate Verdict
In conclusion, TFE and PTFE are not the same. While they both belong to the family of fluoropolymers, there are key differences between them. TFE is a monomer used to produce PTFE, a polymer known for its non-stick properties.
Calling them identical would be like saying a bicycle and a motorcycle are the same because they both have wheels. Remember to handle PTFE with care, as it can release toxic fumes when overheated!